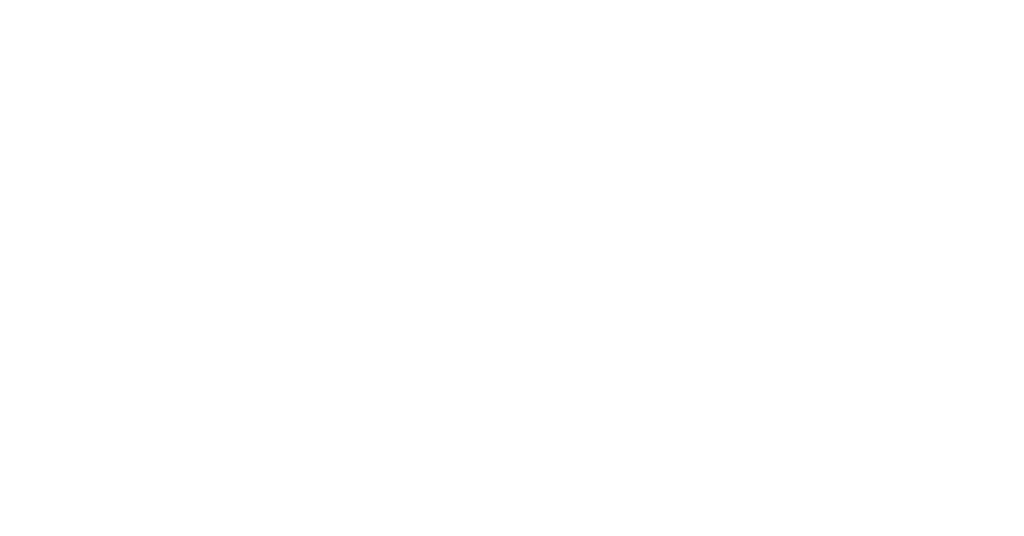
A MCM SpA
success story
MCM SpA leverages Akka to manage concurrency for intelligent manufacturing
Executive summary
MCM group focuses on the design and production of horizontal machining centers and flexible manufacturing systems. Machining Centers Engineering, or MCE, has been the IT division of the MCM group since 1986. Executing their strategy to reimagine factory floors as resilient socio-cyber-physical systems, MCE developed java-Flexible Manufacturing eXecutive (jFMX), an advanced supervisory application designed to enable Flexible Manufacturing Systems (FMS), a computer-controlled production environment designed primarily to adapt to changes such as product details, new products, batch sizes, sequence reordering, and more. FMS relies on automation as much as possible using advanced technology and flexible manufacturing software such as jFMX, resulting in higher overall quality and productivity, lower costs, and less waste.
To create this new superior class of application, which serves as a competitive differentiator for MCM, they turned to Akka to model, integrate, and manage large numbers of concurrent applications. The end result is that the jFMX application enables MCM customers to integrate many process technologies from highly heterogeneous third-party machines into a single intelligent FMS.
The challenge
The MCM group had a vision of integrating the many different information flows involved in manufacturing operations into a single, unified system that could be applied to a diverse set of factory settings. Doing so would enable its customers to interface with a single, reliable, and skilled partner for the design, manufacture, and commissioning of flexible manufacturing systems, making the company a “one-stop shop” for all of its customers’ manufacturing operations needs.
To achieve this, a new class of application capable of integrating the many diverse information flows involved in manufacturing operations was required. With each flow running concurrently, the sheer volume of simultaneous data created incredible complexity, which impacted the performance, system integration, and reliability of manufacturing operations.
The solution
MCM developed a flagship application, jFMX, which leverages Akka to manage the incredible volume of concurrent applications and information flows. Since its introduction, jFMX has evolved into a framework to orchestrate human activities, automation devices, and related tasks. Akka helped to enable this as it allowed MCM to effectively model various components of the production system as concurrent actors, facilitating the coordination of each of these diverse activities. This actor model simplified the management of the complex and simultaneous information flows typical in manufacturing environments. Akka also played a crucial role in helping MCM to evolve jFMX into a framework used to implement a BPMN 2.0 compliant workflow engine, which is at the core of jFMX's orchestration capabilities.
The MCM development team’s journey to Akka evolved from its deep experimentation and use of first Java, then Scala for the initial version of jFMX, before moving to Akka due to its superior capabilities.
By leveraging Akka as the foundation for jFMX, we’ve fundamentally changed the way humans work on the shop floor.
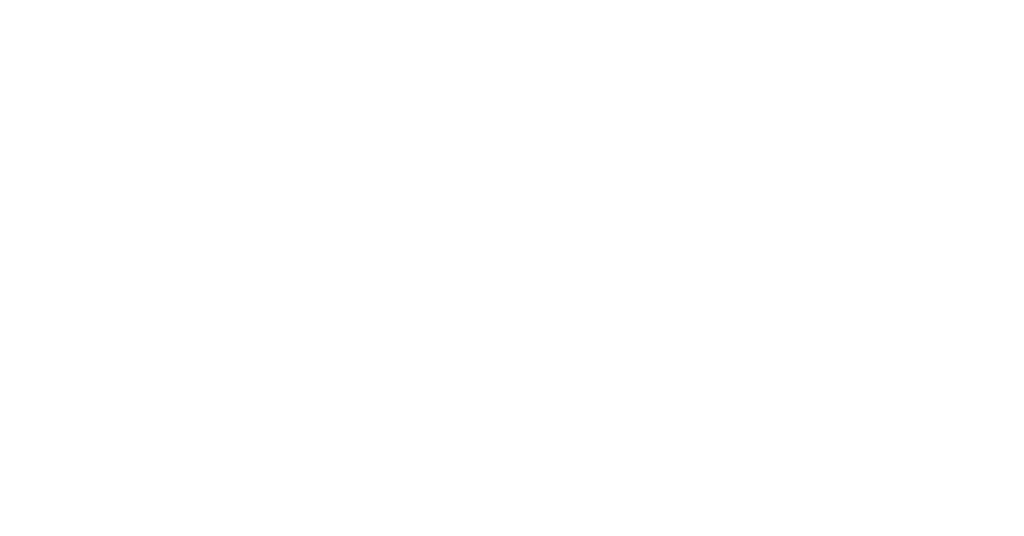
Giuseppe Fogliazza
Technical Manager. MCE
The results
Leveraging Akka gave the MCM development team multiple advantages in building its jFMX application:
- The flexibility to integrate with third-party systems. Each manufacturing customer has a host of third-party systems that need to work together, as well as a unique set of data sources. The jFMX solution is designed specifically to adapt to each individual environment and ensure all systems work together as one. Akka's actor model provided a flexible abstraction that allowed MCM to represent and manage a wide range of heterogeneous components uniformly. Moreover, Akka HTTP facilitated the development of REST APIs, enabling easy integration with various external systems through standard web interfaces. Akka Streams offered a powerful approach to designing and executing data processing pipelines, allowing jFMX to easily adapt to different data sources and integration requirements. Additionally, the event-driven architecture made possible by Akka allowed jFMX to respond flexibly to real-time changes in the production environment, a key requirement for integrating with diverse systems
- A new approach for modeling concurrency to enable high-performance operations. Akka enabled the MCM team to process messages sequentially, avoiding the complexity of managing thread synchronization and locking mechanisms typically found in traditional concurrent programming. This includes the implementation of both synchronous ask patterns and asynchronous protocols between software components.
- Creation of a digital shadow system for predictive analysis. Akka made it possible for MCM’s IT customers to estimate the needs of consumable resources and logistics flows while also guaranteeing the autonomy of the production system.
- An effective implementation of event-based supervisors. Commonly used in manufacturing settings, control systems, and automation, event-based supervisors provide scale, reduce latency, and enable effective resource utilization. Akka made their application possible for jFMX.
- The ability to easily process sensor data. A critical capability for Industry 4.0 use cases, Akka Stream was used by jFMX to simplify the design and execution of data pipelines and information flows from sensor infrastructure.
“By leveraging Akka as the foundation for jFMX, we’ve fundamentally changed the way humans work on the shop floor. We have evolved their role from a simple machine operator to that of a supervisor managing an entire factory-wide system. Our Akka-based applications are a crucial competitive differentiator for our firm,” said Giuseppe Fogliazza, long-time technical manager at MCE.
About MCE, a division of MCM SpA
MCM SpA was founded in 1978 in the area of Piacenza, establishing its origins where machine tools and passion for precision mechanics are tradition. With annual revenue exceeding 100M Euro, the organization focuses on the design and production of horizontal machining centres and flexible manufacturing systems. It serves many application sectors and organizations in the Aerospace, Automotive, Energy, Components, and General Mechanics market sectors. Machining Centers Engineering, or MCE, has been the IT division of MCM group since 1986.